- スクリーンインキ(グラフィック用インキ)
スクリーンインキ(グラフィック用インキ)
スクリーン印刷のメカニズムの大きな特徴は、いろいろの形状の印刷素材に印刷が出来ることである。
このため、紙、合成紙、プラスチックフィルム、プラスチック板、プラスチック成形品、金属、塗装金属、木工品、セラミック類、漆器、ガラス、布などの広範な素材に印刷が行われている。
このように印刷される素材が多いことと、素材の物性や用途適性への対応などによりスクリーンインキの種類は極めて多品種になっている。
従って印刷に際しては、インキの性質を把握して適切な選択を行うことが大切である。
1.スクリーンインキの組成
インキはペースト状になっているが、この中には、インキ皮膜を作る成分(皮膜形成成分:主として樹脂類)、着色剤、溶剤、助剤などが含まれている。
インキの製造工程を図1に示す。
着色剤を含まないインキはクリアーまたはメジウムという。
溶剤を含まないインキは無溶剤型インキである。
水は一種の溶剤であって、有機溶剤の代わりに水を使用したものは水性インキである。

1.1.皮膜形成成分
皮膜形成成分はインキの性能の大半を決める重要な要素である。
この成分によってインキの作業性、光沢、接着性、硬度、可撓性、耐水性、耐油性、耐薬品性、耐候性などの多くの性能が左右される。
皮膜形成成分としては次のようなものがある。
1.1.1.天然樹脂類
シェラック、コーパル、ダンマーなどがあるが使用例は少ない。
1.1.2.合成樹脂類
最も多く使用されている。
大別すると熱可塑性樹脂、熱硬化性樹脂、UV硬化性樹脂などである。
熱可塑性樹脂は、熱により柔軟性が変わる性質の樹脂でこれまでは最も多く使用されてきた。
代表的なものとしては、ビニール樹脂、アクリル樹脂、ポリエステル樹脂、ポリアミド樹脂などである。
熱硬化性樹脂は、熱により硬化する樹脂で一液型と二液型があり、アルキッド樹脂、アミノ樹脂、エポキシ樹脂、ウレタン樹脂などがある。
UV硬化性樹脂は、紫外線により硬化する樹脂で、エポキシ系、ポリエステル系、ウレタン系等の樹脂がある。
近年用途開発が急速に進んでいる。
1.1.3.繊維素系樹脂
繊維素(セルローズ)より作られた半合成樹脂である。
硝化綿、エチルセルローズ、セルローズアセトブチレートなどがある。
1.1.4.ゴム系樹脂
ゴムから作られた半合成樹脂で熱可塑性である。
環化ゴム、塩化ゴムなどがある。
1.2.着色料
着色料としては顔料と染料があるが、主として顔料が使用されており染料は特殊な場合にしか使用されない。
顔料は着色料としての性質の他に、インキに隠蔽性を与え、またインキの耐候性を決定し、耐熱性、耐溶剤性、耐薬品性などに影響を与える。
顔料には無機顔料と有機顔料および体質顔料(フィラー)がある。
無機顔料は鉱物質、有機顔料は非鉱物質で、その比較を表1に示す。
項目 | 無機顔料 | 有機顔料 |
---|---|---|
色相 | 劣る | 優る |
着色力 | 劣る | 優る |
隠蔽性 | 優る | 劣る |
耐熱性 | 優る | 劣る |
耐溶剤性 | 優る | 劣る |
耐候性 | 変色するが褪色少ない | 変褪色しやすい |
価格 | 安い | 高い |
耐酸性 | 安い | 高い |
耐アルカリ性 | 一部を除き劣る | 一部を除き優れる |
無機顔料の主なものは酸化チタン(チタンホワイト)、黄鉛、クロムバーミリオン、紺青、群青、酸化鉄、アルミペースト、ブロンズ粉、カーボンブラックなどであるが、この中の黄鉛やクロムバーミリオンは鉛化合物で毒性が問題となり禁止物質に指定されることが多く、現在は特殊用途以外には使用されていない。
有機顔料は種類が多く、その性質も多様で最も多く使用されている。
表1は一般的な比較であるが、高級有機顔料の中には無機顔料に遜色のない優れた耐候性、耐溶剤性、耐熱性を有するものがある。
蛍光顔料は樹脂に蛍光性染料を結合させて作ったもので、美麗な蛍光色を有しているが着色力、耐候性、耐溶剤性などが劣っている。
体質顔料はインキのフィラーで炭酸カルシウム、硫酸バリウム、カオリン、タルクなどが使われている。
これらのフィラーは低価格なので、インキに添加するとインキの原料費を低下できるが、インキの光沢も低下する。
艶消インキや半艶インキに使用される。
(尚艶消しインキには後述の艶消剤が使われることも多い。)
1.3.溶剤
溶剤は樹脂等を溶解してワニスを作り、インキに流動性を与えてインキを版から印刷素材に転移する“キャリアー”の役目をする。
また印刷時にはインキに添加して粘度の調整をする(希釈溶剤)。
印刷された後はインキ皮膜より蒸発して消失する。
スクリーンインキに使用される主な溶剤を表2に示す。
この表は溶剤を化学構造により分類したものである。
溶剤名 | 沸点 | 蒸発速度比[1] (酢酸ブチル:1) | 引火点 | 管理濃度 | |
---|---|---|---|---|---|
脂肪族 炭化水素 | ミネラルスピリット | 152~204℃ | (0.1) | 39.4℃ | – |
灯油 | 180~300℃ | (0.05) | 40~60℃ | – | |
芳香族 炭化水素 | キシレン | 139~142℃ | 0.7 | 17~25℃ | 100ppm |
高沸点混合溶剤 #100 | 150~170℃ | (0.3) | >38℃ | – | |
高沸点混合溶剤 #150 | 180~210℃ | (0.1) | >65℃ | – | |
高沸点混合溶剤 #180 | 200~240℃ | (0.05) | >82℃ | – | |
ケトン | MIBK | 116.7℃ | 1.6 | 24℃ | 50ppm |
ジアセトンアルコール | 163℃ | 0.14 | 62℃ | 25ppm | |
シクロヘキサノン | 156℃ | 0.23 | 54℃ | – | |
イソホロン | 213℃ | 0.03 | 96℃ | – | |
グリコールエーテル | PGM[2] | 120℃ | 0.71 | 32℃ | – |
ブチルセロソルブ | 171.2℃ | 0.06 | 61℃ | 25ppm | |
エチルカルビトール | 202℃ | (0.01) | 96℃ | – | |
ブチルカルビトール | 230℃ | (<0.01) | 116℃ | – | |
グリコールエステル | PGM-A[3] | 146℃ | 0.35 | 47℃ | – |
ブチルセロソルブアセテート | 191.5℃ | (0.05) | 88℃ | – | |
カルビトールアセテート | 217℃ | (0.01) | 113℃ | – |
- 蒸発速度比のかっこ内の数値は、推定値
- プロピレングリコールモノメチルエーテル
- プロピレングリコールモノメチルエーテルアセテート
溶剤を沸点により分類すると、次のように分類される。
- 低沸点溶剤:100℃以下
- 中沸点溶剤:100〜150℃
- 高沸点溶剤:150〜200℃
スクリーン印刷においては、溶剤を多量に含有している蒸発乾燥型インキが現在でも多く使用されているので、溶剤に関しては充分に留意する必要がある。
溶剤に関し留意する点を以下に述べる。
1.3.1.蒸発速度比
沸点と蒸発速度比とは厳密には一致しない。
表2における蒸発速度比は酢酸ブチルを1としており、これより数字の大きいものほど蒸発が速く、小さいものほど遅いことを示している。
例えばキシレン(0.7)はシクロヘキサノン(0.23)よりも蒸発速度は約3倍速いことを示す。
一般に溶解力の強い溶剤(ケトン系等)は同一沸点の他の溶剤よりも乾燥が遅くなる。
スクリーン印刷において溶剤型インキを使用する際は、絶えず版の目詰まりのおそれがあり、このため中沸点及び高沸点溶剤が使用されているが、この結果として印刷されたインキの乾燥を遅延することとなる。
特にリターダーと呼ばれる超遅乾性溶剤を使用するときは、常温では完全乾燥するまでに長い時間がかかるので充分な注意が必要である。
1.3.2.労働安全衛生法
表2の管理濃度は、労働安全衛生法の有機溶剤中毒予防規則により定められたものである。
管理濃度をもつ溶剤は第二種有機溶剤に該当し、名称の表示、作業環境測定および定期健康診断の実施が義務づけられている。
その他の溶剤にはこれらの義務はない。
1.3.3.危険物
表2の溶剤は消防法の分類では、危険物第四類第2石油類(引火点21〜70℃)または第3石油類(引火点70℃超)となる。
指定数量はそれぞれ1000リットル、2000リットルとなっている。
輸出の際に問題となる国連分類では、引火点60℃以下の溶剤が危険物に分類されている。
従って第2石油類の一部と第3石油類に分類される溶剤は、危険物には該当しない。
1.3.4.(製品)安全データシート
インキを使用する際の安全性についてのデータをまとめたのが、安全データシート(SDS)、製品安全データシート(MSDS)である。
主には溶剤類に関する注意事項をまとめてあるので、インキを使用する際には必ず参照する様お薦めする。
1.4.助剤
インキにはいろいろな助剤が添加される。
助剤添加の目的はインキの性能をさらに改善向上することで、具体的にはインキの印刷作業性を改善して印刷仕上がりの向上を計ることと、インキに要求される物性を補うことである。
助剤添加の効果としては、限定された効果と複合的な効果がある。
例えば紫外線吸収剤は紫外線を吸収する限定効果を与えるが、界面活性剤の中には消泡効果、レベリング効果、レオロジカル効果など複合的効果を与えるものがある。
助剤としては次のようなものが使用されている。(参考:インキ添加剤一覧表)
1.4.1.消泡剤
消泡剤としてはシリコン系、非シリコン系があるが、前者の方が多用されている。
シリコン系消泡剤は微量でも効果があるが、過剰に添加すると重ね刷りの際に上層のインキがはじくことがあるので注意を要する。
印刷面にクリアコーティングを行う場合は、はじきが発生しやすいので、このような用途には非シリコン系消泡剤を使用する。
またシリコン系消泡剤はメジウムに使用するとにごりが発生するので、このような場合にも非シリコン系消泡剤が必要となる。
1.4.2.分散剤
分散剤は、ワニス中に顔料が分散するのを助けるとともに、分散された顔料の再凝集の防止を目的とする助剤である。
顔料分散が良好なインキは、インキの濃度や鮮明度が向上する他に、レベリング性が良くなり色むらの発生が少なくなる。
1.4.3.レベリング剤
インキ皮膜のクレーターやユズ肌などを改善し平滑化する助剤である。
万能型のレベリング剤はなく、インキの種類により効果のあるレベリング剤を選んで添加されている。
1.4.4.腰切剤(チキソトロピック剤)
インキの流動性や曳糸性を減少する効果がある。
腰切剤の適量添加はインキの印刷作業性を向上し画像再現性も良くなるが、過剰に添加するとインキのレベリング性を悪化させ、極端な場合は印刷面に紗の目が現れる。
(UVインキのマットクリアーは、この性質を逆に利用して艶を消しているインキである。)
1.4.5.スリップ剤
インキ皮膜にスリップ性を与え耐摩擦性を向上する助剤で、ポリエチレンワックスやその他のワックス類が使用される。
スリップ剤を加えたインキは爪の引っ掻きにも強くなるので、見かけの接着性が向上するという効果もある。
1.4.6.色別れ防止剤
単一インキに2種類以上の顔料を使用した場合(浅葱等)や、色合わせで複数のインキを混合した場合に、色別れが発生しないようにするための助剤である。
特にチタンホワイトと有機顔料が混合されている場合は、顔料の比重の差や表面物性の差などにより色別れが発生しやすい。
1.4.7.沈降防止剤
インキに含まれる顔料の比重が大きいときに、貯蔵中に顔料が容器の底に沈降してくるのを防止する助剤である。
前述の分散剤、腰切剤、色別れ防止剤などが沈降防止効果を併せ持つ場合もある。
1.4.8.可塑剤
主にビニル系インキの皮膜を柔軟にする助剤で DOP, DBPなどが代表的なものである。
ビニル系以外にも熱可塑性樹脂をベースとした蒸発乾燥型インキに対しては効果があるが、必要以上に添加すると樹脂の軟化によるブロッキングの原因となる。
又、DOP, DBPなどは禁止物質に指定されることが多いので近年はあまり使用されていない。
尚、反応型インキには可塑剤の効果がないので、可塑剤を用いずに皮膜を柔軟にする工夫をしている。
1.4.9.カップリング剤
インキの接着し難い素材、例えばガラスなどに印刷するときにインキにカップリング剤を添加すると、カップリング剤の界面作用によりインキの接着が改善される。
一部のカップリング剤ではポットライフが発生することがあるので注意を要する。
1.4.10.紫外線吸収剤
紫外線吸収剤は紫外線を吸収してインキの耐候性を向上する。
特に屋外用のオーバーコートクリアーなどに添加すると効果がある。
隠蔽性の良いインキではあまり効果がない。
(参考:JELCON VSシリーズ)
1.4.11.艶消剤
インキの艶消剤には炭酸マグネシウムや微粉状のシリカ化合物が使用される。
(参考:JA-450 汎用艶消剤)
1.4.12.硬化促進剤
酸化重合型インキで使用される乾燥促進剤はドライヤーといい、コバルトやマンガンの金属石鹸が使用される。
その他の反応型インキの硬化を促進する触媒類を硬化促進剤として利用する。
(酸化重合型インキは現在十条ケミカルでは製造していないので、コバルトやマンガンの金属石鹸も使用していない)
2. インキの分類と乾燥形式
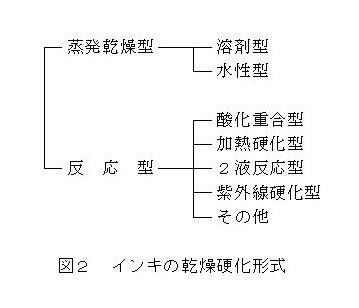
インキを乾燥硬化形式から大別すると図2のようになる。
これらのインキの中で、紫外線硬化型インキ、水性インキは別項にて述べる。
2.1.蒸発乾燥型インキ
過去には最も多く使用されていたタイプのインキである。
インキ中の平均的な溶剤含有量は約50%で、さらに印刷時に希釈溶剤が約10〜30%ほど添加されるので、印刷時のインキ中の溶剤含有量は約60〜65%となる。
このように溶剤含有量が多いので、溶剤の蒸発乾燥には充分留意せねばならない。
インキ中の皮膜形成成分は熱可塑性樹脂で、印刷後溶剤が蒸発すると樹脂が皮膜を形成する。
この皮膜形成の過程は次のように考えられている。
- 溶剤から離れた分子がいくつか集まって核を作る。
- その核に対して分子が結集する(成長)。
- 成長が続いて乾燥小粒が出来る。
- 乾燥小粒が凝集して膜を作る。
このように蒸発乾燥型インキの乾燥は純然たる物理的変化で、この変化は可逆的である。
すなわち、図3のように乾燥皮膜はインキに使用された溶剤によって再溶解される。
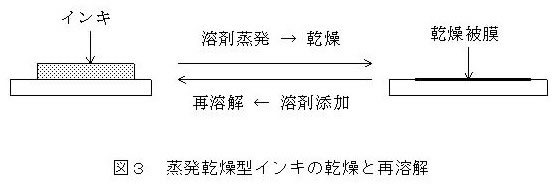
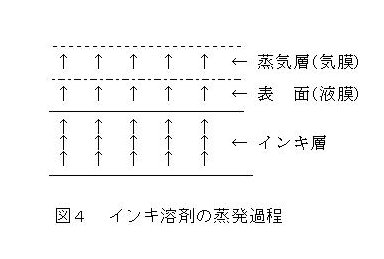
溶剤を含むインキにおいてはまず溶剤の蒸発が起こるが、この蒸発の過程を図4に示す。
インキ中の溶剤はその蒸気圧によって大気中に拡散するため、まずインキ皮膜の表面に出て液膜を作り、次にこの液膜から蒸気化して蒸発する。
この過程においてインキ表面は溶剤の蒸発により当然粘度が上昇するが、それとともに溶剤蒸発により蒸発熱を奪われ温度が低下し更に粘度が上昇してくる。
この結果インキ内部の溶剤の蒸発はだんだん難しくなってくる。
従って乾燥を促進させるためには熱と風が必要である。熱は溶剤の分子運動を活発にすると同時にインキ表面の粘度を低下して溶剤の離脱性を早める効果がある。
またインキ表層に蒸気層が滞留すると蒸発を妨げるので、風を送ってこの蒸気層を除去することが乾燥促進のために必要である。
一般的にいうと、溶剤の蒸発速度はその温度における溶剤の蒸気圧、溶剤と空気の温度差、表面を流れる空気の速さなどによって決まってくるといえる。
しかしながらインキのような分散系においては、溶剤の蒸発速度は上述の要素以外に溶解している樹脂の種類や顔料濃度によって変わってくる。
単独溶剤と分散系中の同一溶剤の蒸発にも違いが出てくる。
単独溶剤は蒸発時間と蒸発量が一定化しているが、インキにおいては時間の経過とともに蒸発量が減少し完全に蒸発するには長時間を要することになる。
逆にいうとインキ皮膜中に長時間溶剤が残留するということである。
スクリーンインキには蒸発の遅い、中沸点及び高沸点溶剤が使用されているので残留溶剤が問題となることが多い。
インキ皮膜中の残留溶剤は可塑剤的な作用で皮膜を軟化してブロッキングの原因になる他、いろいろな悪影響をもたらす。
艶消型インキは若干の残留溶剤が残っていてもブロッキングしにくいので、軟質ビニール用、紙用、PETフィルム用インキなどでは主流となっている。
一方光沢型インキはブロッキングしやすいので特に注意する必要がある。 蒸発乾燥型インキは種類が豊富で取り扱い易く速乾性のため、現在でも多く使用されている。
欠点としては溶剤を多量に使用すること、耐溶剤性、耐熱性などが劣ることである。
紙用、ビニール用、アクリル用、スチレン用、ポリオレフィン用、ポリエステル用、ナイロン用、ポリカーボネート用、布用、木工品用、その他広範な印刷に使用されている
2.2.反応型インキ
皮膜形成成分である樹脂の分子量が比較的小さく、すなわちプレポリマーの状態にあり、これが空気中の酸素、熱、光、触媒などにより、あるいは反応性物質との化学反応により高分子化して皮膜を形成する。
この際に図5のように樹脂相互間で架橋が起こり、新たに生成した樹脂は三次元架橋構造を形成する。
このように架橋構造を作ると、耐熱性、耐溶剤性、耐薬品性などの物性が著しく向上する。
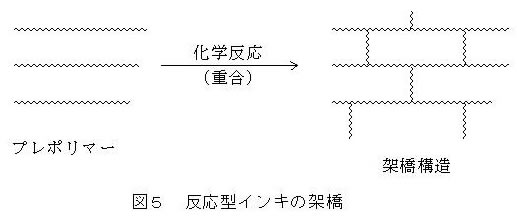
このような反応の速度は反応する物質の濃度が高いほど、また触媒の添加、加熱、光線の作用などのより促進される。
従って反応型インキを使用する場合は加熱が硬化を促進するのに最も効果的である。
このタイプのインキには常温で硬化するものや、一定温度まで加熱を要するものなどがあるが、加熱硬化の場合は印刷素材の熱変形やインキ中の成分の耐熱性を考慮する事が必要である。
反応型インキは反応の形式により次のように分類される。
2.2.1.酸化重合型インキ
一般に油変性アルキッド樹脂を主成分としたインキが使用されている。
このタイプのインキは主成分の油成分に酸素が反応して重合を起こし高分子化する。
この反応は常温ではゆっくり進行するが加熱すると速くなる。
また適量のドライヤーの添加も反応を促進する。このタイプのインキはミネラルスピリットに可溶で、比較的ハイソリッド(高固形分)のため、光沢のある厚膜の印刷が出来る。
接着力は良好で皮膜は強靱である。常温乾燥が遅いことと貯蔵中にインキ表面に皮張りを起こすのが欠点である。
塗装金属、木工品などの印刷に使用されるが、スクリーンインキの主流ではない。
(このタイプのインキは現在十条ケミカルでは製造していない)
2.2.2.加熱硬化型インキ
加熱硬化型インキは、常温では硬化せずに加熱により硬化するタイプのインキである。
アクリル系、エポキシ系、アミノ・アルキッド系樹脂等を使用したインキ、及びブロックイソシアネート樹脂を使用したウレタン系インキがある。
硬化機構は樹脂分子の活性基(官能基)が熱により反応し架橋して効果する。
これらのタイプのインキの熱硬化には通常120〜180℃で20〜30分を要する。
主に金属素地、塗装金属、ガラスなどの印刷に使用され一部はプラスチック成形品(熱硬化性プラスチック又は耐熱性プラスチック)の印刷に使用されている。
このタイプのインキは、印刷時に硬化剤を混ぜる手間がかからずポットライフもないので、印刷作業は簡便である。
しかし高温加熱が必要なので、耐熱性の低い一般プラスチックには使用出来ない。
ガラス、金属用としては、2液型インキと同等かそれ以上の皮膜物性を持つ。
(#2500 遅乾性MIG-Nインキ)
2.2.3.2液反応型インキ
2液反応型インキはインキと硬化剤がセットになっており、使用時に両者を一定比率に混合して印刷を行う。
混合によりインキ中の樹脂と硬化剤中の樹脂が反応して高分子化する。
この反応は常温ではゆっくりと進行するが加熱すれば速くなる。
このようにインキと硬化剤を混合すると反応が起こり高分子化が進んで、その結果インキ粘度が増大してくるので、混合インキは可使時間(ポットライフ)内に使用せねばならない。
この可使時間はインキ、硬化剤の種類により異なるが、通常7〜8時間は最低必要である。
2液反応型インキはハイソリッドで光沢の良い厚膜印刷が出来る。
通常の蒸発乾燥型インキが接着し難い素材に接着し、その硬化皮膜、特に加熱硬化した皮膜の諸物性は優れている。
エポキシ系、ウレタン系のインキが代表的で金属素地、塗装金属、熱硬化樹脂製品、ガラス、処理ポリエチレン、処理ポリプロピレンなどのシートや成形品などの印刷に使用される。
(#1000 エピライト、#2000 AP、APGインキ、#9300 HIPET)
2.3.その他の反応型インキ
2.3.1.フッ素樹脂系インキ
近年スクリーン印刷分野においても屋外曝露5年以上の耐候性を要望するケースが出てきた。
フッ素樹脂系インキはこの要望に応えるべく開発されたインキである。
このインキは2液型で常温硬化、加熱硬化が出来る。皮膜形成樹脂はフルオロエチレンビニルエーテルのようなフッ素を含んだ樹脂である。
この樹脂のワニスと最高級顔料にてインキを作り、印刷時に硬化剤と若干の硬化促進剤を混合して印刷する。
硬化は常温にて7日以上、80℃にて約2時間、130℃にて約20分である。硬化インキは光沢が良く、耐候性、耐摩擦性、耐薬品性が優秀である。
金属、アクリル、ビニールステッカー、硬質ビニール等に接着する。
フッ素系インキの色物を印刷しその上にフッ素系インキのクリアーをオーバーコートすると5年以上の屋外曝露に耐える。
また通常の耐候性インキ(主にアクリル系)の印刷面にこのクリアーをオーバーコートすると著しく耐候性を向上することが知られている。
高価なフッ素系インキの色物を使うよりも、通常の耐候性インキを使う方が経済的なため、オーバーコートクリアーのみフッ素系インキが使われるケースが多い。
(セレクトSLFオーバーコートクリアー)
2.3.2.シリコン樹脂系インキ
フッ素系インキと同様の目的で使用されるインキである。
樹脂成分はアクリル系シロキサン架橋反応性樹脂で硬化剤を配合して使用する2液型である。
フッ素系に準じる耐候性を有しており、低温硬化性で価格はフッ素系よりも安価である。
(このタイプのインキは現在十条ケミカルでは製造していない)
3.インキ各論
主な素材へのインキの概要と注意事項を述べる。
3.1.紙用インキ
紙用インキには版の形式によって2種類がある。
1種類はラッカー原紙を使ったカッティング版用のインキで、ラッカー原紙を侵さないミネラルスピリットを溶剤成分としたインキである。
蒸発乾燥型と酸化重合型インキがある。
もう1種類はグリコールエーテル系溶剤を使用した蒸発乾燥型インキである。
通常紙用インキは紙以外に発泡スチロール材の印刷に使用する場合が多いので、この素材を侵さないグリコールエーテル系溶剤が使用される。
紙用インキには光沢型と艶消型がある。
価格面より中級以下の顔料を使用しているので耐候性に注意することと、染料系の顔料(染色レーキ)を使用している品種もあるので色素の移行(マイグレーション)に注意せねばならない。
木工品素地や布製立看板の印刷にも紙用インキが使われることが多い。
(#200 Qセット、#600 VACカラー)
3.2.ビニール用インキ
ビニールは可塑剤の含有量により軟質と硬質がある。
軟質ビニールフィルムは可塑剤を多量に含有しており、これが生地表面に浮き出ると接着不良やブロッキングの原因となる。
このような場合は生地の表面をアルコールなどで拭いて可塑剤を除去せねばならない。
軟質ビニール用のインキはビニール共重合樹脂を主成分とし、顔料は色素の移行(マイグレーション)を起こさないような耐溶剤性、耐可塑剤性の優れたものを使用している。
軟質ビニールは柔軟性なので一般の印刷機では印刷が難しく、ほとんどが長台捺染印刷である。
このためインキは速乾性の半艶ないしは艶消型である。
可塑剤の含有量の少ないステッカー類の印刷にはビニール系、アクリル系のインキが使用されているが、屋外用が多いので耐候性に注意する必要がある。
硬質ビニールの印刷にはビニール系、アクリル系のインキが使用されているが、アクリル系は光沢と耐候性に優っている。
印刷作業性はビニール系が優る。
(ビニールインキ、#3500 EXGインキ、#100 スーパーグロス、#600 VACカラー)
3.3.アクリル用インキ
看板、ディスプレー、成形品、計器板などに印刷が行われている。
屋内用を除き耐久製品が多いのでインキも相応した高物性のものを使用せねばならない。
インキはアクリル樹脂を主成分とし高級顔料が使用されている。
使用に際しては耐候性、真空成形性などを、また計器類はそれぞれの仕様規格を考慮してインキを選定する。
ABS樹脂の印刷はアクリルと同様に行えばよい。
(#100 スーパーグロス、#600 VACカラー、#8100 SNAP、#1700 HIT)
3.4.ポリオレフィン用インキ
ポリエチレンやポリプロピレンを総称してポリオレフィンという。
スクリーン印刷においてはフィルム類の印刷は少なく、主にシート類や成形品の印刷が多い。
ポリオレフィンは、それ自体が不活性物質なのでインキの接着性が良くない。
従って表面処理を行ってから印刷する必要がある。
表面処理法としては、シート類はコロナ放電処理を行い、成形品はフレーム処理を行うのが一般的である。
このような表面処理によりポリオレフィン材の表面が酸化されて活性化(極性)される事によりインキの接着が改善される。
インキは蒸発乾燥型、2液反応型、加熱硬化型、紫外線硬化型がある。
蒸発乾燥型インキは以前はゴム系のものがシート類の印刷に多く使用されたが、耐油性、耐候性が悪いため現在はあまり使われない。
代わりに塩素化ポリオレフィン樹脂が使われている。
2液反応型インキは、エポキシ系とウレタン系がシート類や成形品に使用される。
ポリオレフィン製ボトルへの印刷にはUVインキが使用されるケースが多い。
(#5600OPS、#2000AP)
3.5.ポリエステル用インキ
ポリエステルはPET(ポリエチレンテレフタレート)が代表的な印刷素材である。
フィルム、ステッカー、成形品などへの印刷が行われているが、特に工業計器類への利用が多い。
インキはポリエステル系の樹脂を主成分とした蒸発乾燥型インキが主に使われており、接着性、耐候性、耐油性、耐アルコール性、耐薬品性などが良好である。
一部の高度な物性が要求される用途には2液反応型インキが使われるケースもある。
処理ポリエステル材には専用インキ以外のインキ(ビニール用、アクリル用)も使用可能である。
(#900テトロン、#9000PET、#9100PLPET)
3.6.ポリスチレン用インキ
ポリスチレン、ハイインパクトスチレン、AS樹脂は、シート、成形品、発泡材として印刷が行われている。
これらの材質は耐溶剤性が弱いので印刷に際しては材質を溶かさないインキと希釈溶剤を選定することが大切である。
インキはグリコールエーテル系溶剤への可溶樹脂を主成分とした蒸発乾燥型インキが使用される。
適性インキで印刷しても尚クラックが発生する場合には、材質をアニール処理する必要がある。
(#800PAS)
3.7.ポリカーボネート用インキ
ポリカーボネート材は優れた物性により工業計器類へ利用され印刷が行われている。
耐溶剤性が劣るのでインキや希釈溶剤によりクラックが発生する場合がある。
耐溶剤性は逐次改善されており、以前よりはインキと希釈溶剤の選択幅が広くなってはいるが、注意は依然必要である。
工業計器への印刷が大部分なので、用途に応じた仕様規格へ合格するインキ物性が必要である。
CD、CD-ROM、CD-R、DVDなどもポリカーボネート材で出来ているが、インキは全てUVインキが使用されている。
自動車計器板へのUVインキの使用も増えている。
(#8000PC、#8100SNAP、#1700HIT)
3.8.金属、ガラス用インキ
金属では、金属素地への印刷は少なく、塗装金属面への印刷が多い。
金属、ガラス共に反応型インキが多く使用される。
(#1000エピライト、#2000AP、APGインキ、#2500遅乾性MIG-Nインキ)
3.8.1.アルミ用
2液型のエポキシ系やウレタン系のインキが多く、熱硬化型インキも使用される。
3.8.2.メラミン塗装金属
酸化重合型、2液反応型、熱硬化型インキが使用される。
一般的にインキの諸物性は、酸化重合型→2液反応型→熱硬化型の順に良くなる。
3.8.3.熱硬化アクリル塗装金属
金属の高級塗装である。
インキとしては熱硬化アクリル系インキ、2液型ウレタン系インキがよい。
塗装の焼き付け温度によりインキの接着性に差が出るので注意が必要である。
高温焼き付けされた塗装面に印刷する場合には、インキも同等の高温で焼き付けないと接着不良になる場合がある。
(APGインキ、#2500遅乾性MIG-Nインキ)
3.8.4.プレコートメタル(PCM)
プレコートメタルとは、成形や組立などの加工を行う前に、連続塗装ラインであらかじめ塗装した金属材料である。
カラートタンや塩ビ鋼板などがこれである。
これらの印刷には、塗装されている塗料のタイプに応じてインキの選定を行えばよい。
3.8.5.ガラス
2液型のエポキシ系インキが多く、熱硬化型インキも使用される。
(#1000エピライト、#2500遅乾性MIG-Nインキ)
3.9.木工品用インキ
木工品素地と塗装木工品の印刷がある。
3.9.1.木工品素地
素地にはたいていのインキが接着するが、素地へのインキの滲みこみがあるので、なるべくハイソリッドなインキを使用するのがよい。
酸化重合型、2液反応型、ハイソリッドのアクリル系インキなどが使われる。
3.9.2.木工品塗装面
木工品の塗装には、アルキッド系塗料、不飽和ポリエステル系塗料、硝化綿ラッカー、アクリルラッカー、ビニールラッカーなどが使用されている。
アルキッド系、不飽和ポリエステル系塗料の塗装面には通常酸化重合型インキが使用され、その他の塗装面にはアクリル系、ビニール系インキが使用される。
3.10.布用インキ
主には防水ナイロン布と綿布に印刷が行われる。
3.10.1.防水ナイロン布
防水処理の程度により、インキの接着性に差がある。
一液又は二液型ウレタン系インキが使用される。
(#7000NSP)
3.10.2.綿布
Tシャツやトレーナーなどの印刷にプラスチゾルインキや水性インキが使用される。
参考文献
- スクリーン印刷技術(株)総合技術センター(H5.4)
- 十条ケミカル社内資料、その他