- 色合せの進め方
色合せの進め方
印刷作業における色の問題は、黄、紅、藍、墨の4色を使う網点のプロセス印刷(カラー分解)と、印刷会社が得意先から指定された各種の指定色の2つに分けられる。
前者の場合にはインキ会社が設定しているカラー分解用のハーフトーンインキが使用される。
色合せの作業が行われるのは後者の場合であり、色々の指定色が作られる。
インキ会社では、印刷会社で簡単に色合せが出来るように色合せの処方例を掲示した見本帳を用意している。
しかし色の数は無限であるから得意先から指定された色に合致するものが含まれているとは限らない。
この場合には、適当なインキを混ぜ合わせる事によって指定された色を作り出す色合せ作業(調色作業)が必要となる。
インキ会社に色見本を渡し、色合わせ作業を委託する例も多いが、この場合には一般的に標準インキの価格より高くなるし、 時間もかかるので、印刷会社内での色合せ作業がもっと行われても良いと考える。
色合せ作業は、ある適当な何色かの原色インキを混ぜて指定された色を作り出す事であるが、身近かにあるインキをむやみに混ぜるわけにはいかない。
なぜなら、インキには色々な素材用の多くのシリーズがあり、一般には違うシリーズのインキ同士は混ぜられない事、 印刷物が色々な後加工をされる事、又印刷物の用途が多様化しており様々な耐性が必要になるケースが多い事などから、 色合せは単に色が合致すればよいという事ではない。
後で問題を起こす事がない様に、素材への接着性や耐性についても十分考慮されたインキシリーズの原色インキを選択し、色合せ作業を行わなければならない。
1.色合せを進める前に
(1)色とは何か
私達の周りには、私達が直接関係している印刷物をはじめ、人工あるいは天然の非常に多くの色が存在している。
われわれが色を感知する第一条件は、色光の存在である。
色光はX線、紫外線、赤外線あるいは電波など同じように電磁波の一種である。
これらはそれぞれの波長によって区分されるが、電磁波のうち400nm(ナノメーター、1nmは100万分の1ミリ)から700nmの波長域のものを色光あるいは可視光といって、人間の眼に色を感じさせるものである。
赤外線は可視光の赤の端、 770nmから0.4mmまで可視光ととなり合った長波長域のものであり、紫外線は可視光の紫の端、380nmから10nmまで可視光ととなり合った短波長域のものである。
可視光の最も一般的なものは太陽光に含まれるものであり、虹の現象、あるいはプリズムでの太陽光の分解などから太陽光には赤色から紫色に かけての色光が含まれている事が分かる。
この事は400nmから700nmにかけての色々の波長の色光が混じると白色光になることを示している。
400nmから700nmの可視光の波長による色の差は、表1の通りである。
波長(nm) | 色光 | 光の三原色 |
---|---|---|
400~450 | 紫色光 | 青紫色光 |
450~500 | 青色光 | |
500~570 | 緑色光 | 緑色光 |
570~590 | 黄色光 | |
590~610 | 橙色光 | 赤色光 |
610~700 | 赤色光 |
太陽光、その他の光源からの光には、色々の波長の色光が混じっていて、この光がある物体にあった時、その物体によりある波長の 色光が選択的に吸収され、残りの色光が透過あるいは反射されて眼に色を感じさせるのである。
リンゴが赤く見えるのは、リンゴの表面が赤以外の 色光を吸収し、赤色光を反射するからである。
リンゴに赤色光を全く含まない青色光をあてると、青色光は吸収されてしまい、リンゴは黒く見えるようになる。
インキの色をつかさどる素材は顔料(あるいは染料)で、印刷面に光があった時に、これら色料が光の中のどの成分を選択的に吸収するかによって、 各種の色が眼に感じとられることになる。
可視光を400nmから500nm、500nmから600nm、600nmから700nmと3つに分けてまとめてみると、表1のように、それぞれ 青紫色光・緑色光・赤色光となり、これが光の3原色(RGB)である。
青紫色光と緑色光が加わるとシアン(藍)、緑色光と赤色光が加わるとイエロー(黄)、青紫色光と赤色光が加わるとマゼンタ(紅)となり、 全部が加わると白となる。
これを加法混色(加色混合)といい、簡単にいえば加える色光が多くなればなるほど、色が明るくなる。
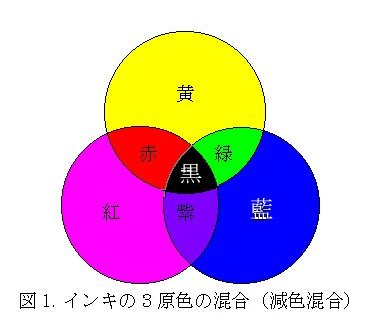
インキの3原色は、黄(イエロー)・紅(マゼンタ)・藍(シアン) である。
この3原色はいずれも白色光から光の3原色の1色が吸収され取り除かれた色である。
例えば、黄は白色光から青紫色光を 除いた500〜700nmの範囲の色光の色であり、紅は白色光から緑色光を除いた400〜500nmの範囲と、600〜700nmの範囲の色光とから成る色であり、 藍は白色光から赤色光を除いた400〜600nmの範囲の色光の色である。
黄インキと藍インキを混ぜると緑インキ、黄インキと紅インキを混ぜると 赤インキ、紅インキと藍インキを混ぜると紫インキとなる。
これを減法混色(減色混合)といい、 混合する色が多いほど、出来た色は暗くなる。
この事は色合せで新しい色を作る時の最も基本になる事項である。
色には色感覚の基本的な性質として色相・明度・彩度という性質があり、これを色の3属性という。 「色相」とは赤、緑、紫といったように色あいの違いの事である。
「明度」は明るい色であるとか、暗い色であるという明るさの度合を示し、 明るい色の事を明度が高い、暗い色の事を明度が低いという。
白は最も明るく、黒は最も暗く、その間に色々の明度差のある灰色が入ってくる。
各種の色相の色にも明度の違いはあり、同じ赤でも黒ががった赤と、そうでない赤とで明度差がある。
色相、明度が同じでも、あざやかさの違いがある。
白、灰、黒などにある色相のインキたとえば赤を少しずつ加えてゆくと、次第にあざやかさの増した赤色が作られる。
このあざやかさの段階を 「彩度」といっている。
よりあざやかな色を彩度が高い、あざやかさの少ない色を彩度が低い。
白、灰、黒は彩度がゼロなので無彩色という。
色合せを進めて行く時、見本色に対して色相が違うのか、明度が違うのか、あるいは彩度が違うのかという事を考えながら進める事が大切である。
(2)同じ色だということの意味
色合せは指定された色と同じ色のインキを作る作業であるが、その色が合っているかどうかの判定は主に眼による「視感判定」で行われる。
電子工学や測色理論が高度に進歩している現在では、測色機とコンピューターを組み合わせたコンピューターカラーマッチングシステム(CCM)が、 一部の色材分野では採用されている。
インキ分野での応用例もあるが、主流としては現在でも視感判定で見本色との比較をしながら色合せをしている。
色の差を数字化して表す色差計、ある色がどのような色光の成分から成っているかを測色し、あるいは数字化できる分光光度計の使用などによって色の解明も行われるが、これらを色合せ作業の中にとり入れることは現状ではまだ難しい。
かえって熟練した作業員の判断の方が、 時間が早く且つ正確である。
磁性インキ印刷物等の特殊な印刷物には各種の識別装置が使用されるが、本やポスター等、ほとんど全ての印刷物は人間の眼に訴える目的を持って作られている。
その意味では視感判定は最良の方法といえる。
人間の眼は光の3原色を感じとる神経を持っており、色の微妙な差を感じとる識別能力は非常に高い。
しかし全ての人に同じような視感判定結果を期待することは出来ない。
運動神経が個人個人で差があるように、色の判定能力にも相当の差がある。
年齢差があり、高齢になれば能力が低下する。
又その時の体の状態によっても影響されるなど、運動能力と同様である。
色合せ作業は経験とカンに支配される面が多く、作業の進め方の速さにも個人差があり、その熟練によっても色の判定能力は違ってくるが、 本来の個人差も無視出来ない。
人によって色神経の持ち方に差があり、ある色に対してより微妙な識別をする例も多い。
従って場合によっては 視感判定だけで、この色は全く同じであるという結論を得るのは難しい事もある。
視感判定は精度がかなり高く、手軽な方法ではあるが、記憶が出来ない、再現性に欠ける、数値化出来ないなどの欠点があり、客観性には乏しい。
これを補うものとして色差計や分光光度計などの測色計による測定値が活用されるのである。
(3)色合せをする際の注意事項
インキの色合せとは、インキの肉色を合わせるのではなく、印刷された後の乾燥皮膜の色を合わせるということに注意を払わないといけない。
その他色合せを始める前に確認しておくべき注意事項は次の通りである。
- 印刷されたインキ皮膜の厚さによって色が違ってくるので、インキ膜厚は一定にしなければならない。
- スクリーン印刷では、実際には機械刷りで印刷されるインキを、手刷り印刷で色合せする事が多いと思われるので、特に注意しなくてはならない。
- 透明性の高い色では、膜厚の差が即濃度差になってしまう。又黒生地用の高隠蔽性色の場合にも膜厚の影響は大きい。
- 印刷された直後の、インキが未乾燥状態の時に色を調べる事は、避けた方がよい。
- 艶消型の インキは未乾燥の状態の時には光沢があるので、この状態で色合せをするのは論外である。
- 光沢型及び半光沢型インキの場合も、インキ皮膜が乾燥した後の平滑性・光沢・ブロンズといった皮膜性状が、色に影響を与える。
- 遅乾性のインキや反応型のインキの場合特に注意が必要となる。
- 硬化に 時間のかかる反応型インキは、調色作業にも長時間を要することになるのでやっかいである。
- 未乾燥の状態で同じ色であったインキでも乾燥後、若干の光沢差を生じる場合、光沢がある方が色がさえて見え、光沢のない方が色がくすんで見え、色の差が生じる。
- 従って色をみる場合には、光沢が同じ程度かどうかをよく確認する必要がある。
- 繰り返しの注文品の場合は、どのインキを 、どれくらい使って色合せしたという事が分かっているので、未乾燥状態で標準品と比べて判定する事もある程度は出来る。
- しかし混合インキの色数が多い時や、微妙な中間色の場合にはやはり乾いた後での確認が必要である。
- いずれにしても間違いを無くす為に、乾いた後で色を調べる事が安全な方法である。
- UV硬化型インキは、UV照射機を通す事で瞬間的に硬化するので、このような問題は発生しない。
- ただし一部のUVインキは、UV照射機を通したときに一時的に黄色又は褐色に変色し、時間の経過と共にまた元の色に戻る性質を持つものがあるので、同様な注意が必要となる。
- ブロンズも色を見る時やっかいなものとなる。
- ブロンズは高濃度の金赤インキや紺藍インキが乾燥した後、そのインキ皮膜表面に出る金色のような輝きである。
- ブロンズの影響でインキ本来の色を見誤る恐れがある。
- 光沢を強調したグロスインキには、ブロンズはない。
- ブロンズの出ているインキ面にオーバーコートクリアをかけると、ブロンズは見えなくなる。
- インキの製造後の時間 経過によってブロンズの発見具合が変ることもある。
- このようなブロンズ色まで色合せする事は難しく、多少の色の差は許容しなければならない。
- 後でオーバーコートクリアがかけられる場合は、色合せの段階でもオーバーコートクリアをかけて、ブロンズを消してから正しい色に合せる必要がある。
- ビニル引きやラミネーションによってもブロンズが消えるので、これらの加工が行われる場合もブロンズを消しての色合せが必要である。
- インキの透明度(隠蔽性)が違うと、下地の影響で、同じ色であっても違った色感を与える。
- 透明度の高いインキは、不透明なインキに比べ着色力が同じであってもうすく見えるので、色合せではインキの透明度も合せる必要がある。
- 黒など の暗色系の生地の上に、彩度、明度の高い隠蔽性色を印刷しなくてはならない場合に特に問題となる。
- 以前は黄鉛(黄)やクロムバーミリオン(朱)等 の隠蔽性の優れた無機顔料を使ってこれに対応する事が出来たが、最近では安全性や環境問題の面からこのような顔料は使用されない。
- これらの 顔料を使った見本に合せる時は、隠蔽性を正確に合致させる事は難しく、若千の色感の違いは、認めてもらわなければならない。
- 又黄・赤系の色の 場合には、隠蔽性の有機顔料を使用したオペーク色(EXOインキ)が使用できるが、藍・グリーン系色の場合には 、チタン白を使った白インキの添加で不透明化する事になるので、色相はくすみを生じる。
- フィルムに印刷する用途では、裏刷りを指定される事が多い。
- この場合にはフィルムを通し てみた色を標準見本に合わせなくてはならない。
- この場合もちろんフィルムは指定のものを使用しなくては色は合わせられない。
- 更に指定色の上に 別のインキを印刷(裏押え印刷)し、この裏のインキの影響を受けた状態で色合わせをしなくてはならないようなケースもあり、非常に手間のかかる色合せである。
- 尚裏刷りの場合には、光沢を合わせる必要がないので、印刷作業性の優れた艶消型インキ が使用されることが多い。
- 自動車の計器盤用のインキなどでは、透過色の色合せを行わなくてはならない。
- 一般に反射光 の色が合っていても、透過光の色が合っているとは限らないので注意が必要である。
- 透過光の色合せ作業には、ライトテーブルを使用する。
- ライト テーブルの光源は指定のものを使わなければ、色が合っているかどうかの判断が出来ない。
- 更に最近は、輝度計で測定した輝度値を合わせることまで要求されるケースがあり、やっかいである。
- 照明光の選択も大切である。
- インキに使われている顔料が、色光を選択的に吸収・反射する事によって色が感じられるのであるから、照明光の性質は非常に重要である。
- 照明光としては自然の太陽光、人工の白熱灯、蛍光灯の光等があるが、これらの光の色光成分は相当な違いを持っている。
- 厳密にいうと同じ 白熱灯、蛍光灯でも新しいものと長時間使ったものとでは色光成分は異なり、太陽光も朝と昼、場所、天候などで大きく変化しており安定した照明光とはいえない。
- 特に夕方の太陽光は色光成分が変化し、明るさも不足してくるので色合せの照明光としては不適当である。
- 一般には、自然の太陽光が標準的な光源として使われている。この場合も、室内の間接光のもとで行うのがよい。
- 直接光で色をみると、インキからの反射光が強すぎて、眼の神経を刺激するため正しい色の評価が出来なくなる。
- 明るい昼間の室内で、出来れば北向きの窓からの光で色をみるのがよい。
- 最近の室内照明光は蛍光灯が主体となっているが白色光、昼光色その他多くの種類があり、それぞれ色光の含み方に差があるので注意が必要である。
- 印刷物の色を調べる為に、よりよい色光成分を考慮した日本印刷学会推薦「色評価用蛍光灯」が容易に入手出来るので、これを使う事が好ましい。
- 色には、メタメリズム(条件等色)という複雑な性質がある。
- これは、ある照明光の下では 同じ色に見える2つの色が、別の照明光の下では違った色に見える性質である。
- 数種のインキを混ぜて色を出す場合、特に茶、オリーブ、灰色などの中間色でよくこの現象がみられる。
- これは見本に使われている顔料の分光特性と、色合せに使っている顔料の特性が違っているために起こる現象である。
- 完全な色合せは、同一の顔料を使ったインキを使わないと出来ない。
- 夜間、あるいは良い条件の照明光が得られない所で色合せをする時は、メタメリズムによる色違いの問題が起こりやすいため各種の標準光源を組み合せて使う事が勧められる。
- 標準光源を使えば常に一定の照明下で色を見て、判定出来るので問題発生を防ぐ事が出来る。
- 標準光源には色々のものが、一般的にはA光源・B光源・C光源があり、その色光の内容は表2の通りである。
- 白色光蛍光灯はほぼB光源に、昼光色蛍光灯はほぼC光源に相当する。なお印刷物の「色評価用蛍光灯」は、色温度が5000゚Kとなっている。
- メタリズムを注意する点からいえば、これら全ての照明光下で色を見て、同じかどうかを判定する必要があるが、実際のところ全ての照明光下で色を合致させる事は難しいので、色合せ作業では標準的なものとして「色評価用蛍光灯」を使用する事が勧められる。
- 照明光については、色光成分と同時に明るさも大切な事である。
- うす暗い所では、色を正しく見る事は出来ず、明るすぎても刺激が強すぎて正しく色を見られない。
- 色を見るには適当な明るさ(照度)が必要である。
- 上限が1500ルックス、下限1000ルックスの照度がよい。
- これは40ワットの蛍光灯2本を並べた時の 1m真下における明るさに相当する。
- 印刷物の発注元との色のトラブルを避ける為には、発注元のデザイナーが指定色を決定する際の照明光を確認し、これに合わせた条件下で色合せをしなくてはならない。
- この際には、上記の「色評価蛍光灯」を両者共に使用する事を勧める。
標準光源 | 性質 | 色温度 |
---|---|---|
A光源 | 白熱(タングステン)電灯の光 | 2854゚K |
B光源 | 太陽の直射光を代表するランプ | 4870゚K |
C光源 | 青空の光を代表するランプ | 6740゚K |
D65光源 | 分光測色計の標準光源 | 6500゚K |
2.色合わせの進め方
何に印刷するのかという印刷素材、どんな機械でどのように印刷するのかという印刷条件、どのような効果を希望するのかという印刷効果、 印刷後の印刷物はどのように加工処理されるかという後加工処理、最終製品として何に使われるのかという用途などを十分考慮して適正なインキを選択し色合せしなければならない。
- 印刷素材
- 繰り返しの注文で前回インキの印刷見本がある時は、これを使って同じ色を つくり出すように進めていけばよい。
- メーカーやタイプの違うインキ、あるいは印刷物や色票が見本として与えられた場合には、実祭の印刷に 使われる生地で色合せする必要がある。
- 例えば、CDの鏡面上に印刷したときの色相は、他の材質の上で再現することは難しい。
- 又、紙の刷見本 の色が、黒色プラスチックの上では再現出来ない事がある。
- 生地の差がインキの色に及ぼす影響は大きく、生地の色、光沢、又性質の違いから来るインキの転移量、膜厚、インキの吸収性、乾燥皮膜 の形成状況などの多くの条件が色に影響する。
- スクリーンの場合は印刷素材が非常に広範囲で、その種類によってインキタイプが違うので、 印刷素材の確認が重要である。
- 更に、離型剤その他の添加剤の有無、前処理の有無なども調べる必要がある。
- 印刷条件
- 印刷に関する全ての条件が色に影響を及ぼすが、特にインキの転移性と膜厚の 影響が大きいので、印刷方式にまず注意しなければならない。
- インキの膜厚は、平版(オフセット)→凸版→グラビア→パッド→スクリーン→ (塗料)の順で厚くなる。
- 凸版なら容易に出せる色が、平版では出せなかったり、逆に平版ではなめらかなインキの着肉が得られるのに、凸版では モットリングなどにより色の感じが合わない事がある。
- 各々の印刷方式で適正なインキ盛りと濃度で色合せしなくてはならない。
- 又、どのような 図柄で印刷されるのかも注意する事の一つである。ベタ刷か、アミ刷か、両者の組み合せか、白ヌキの大小、刷順などによってインキの盛りに 限度が生ずるため、それに応じた濃度の調整や、流動性も考えなくてはならない。
- グラビアインキやスクリーンインキでは希釈溶剤の使い分け による乾燥性の調整も必要となる。
- スクリーン印刷の場合には手刷りで仕上がり色の確認を行うが、厳密に言えばこのインキを機械刷りした場合 には仕上がりが変わって来る可能性がある。
- 印刷効果
- 色、濃度、透明性、光沢、調子の再現性、重ね刷りの状態、オーバーコート クリアの有無などに注意する。
- インキや色の種類によっては、耐性面の制約などから、希望通りの印刷効果が得られない場合もある。
- 後加工処理
- 印刷物が何らかの後加工が行われて最終製品になるものが多い。
- 質ビニール のウェルダー加工、アクリル板の真空成形、金属素材の焼き付け、仕上げ塗装、高圧蒸気・高圧熱湯処理、一般印刷物でのビニル引き、ラミネーション、パラフィン浸漬、熱成形、製袋・製函、内容物殺菌、箔押しなど多くの加工工程があり、多種多様な加工機と加工用材料が使われるので、 これら条件の十分な確認と同時に、適正なインキを選択する必要がある。
- 最終製品の用途
- 印刷物が最終的にどのような形態で、どんな用途に使われるか、その用途 上要求される諸耐性とその程度などを十分に調査し、適正なインキを使わなければならない。
- 用途段階でのトラブルは補償なども非常に大きく、 重大なものとなるので念には念を入れて調べる必要がある。
- 石けん、殺虫剤、肥料、油性食品などの包装印刷物では、耐アルカリ性・耐水性・ 耐候性・耐薬品性・耐油性などが要求される。
- 看板、屋外ディスプレー、ポスター、ステッカー等への印刷では 耐候性が要求される。
- 化粧品等の容器の印刷では、耐摩擦性・耐内容物性が必要とされる。
- 又特に自動車計器盤や家電製品等の工業製品の 印刷では、耐候性・耐熱性・耐湿性・耐熱サイクル性・その他多くの物性が要求される。
- 尚調色インキの耐候性 は、原色インキの場合よりも低下することがあるので注意を要する。
- 食品包装材料や玩具類への印刷の際には衛生安全面での考慮が要求される。
- この様に製品の種類によって要求される条件は千差万別であり最も適切なインキを選択する必要がある。
- 不明な点はインキ会社に相談し、必要に よってはさらに耐性のよいものを入手するなど万全を期す必要がある。
以上の5つの要素、特に耐性の面から使用材料に制約を受けることがあり、指定された色に合せる事が難しい場合がある。
耐候性が弱い鮮明な色 のインキを使用している指定色の場合、耐候性の強いインキで色合せをしても鮮明性が不足する事がある。
蛍光色は耐候性が劣る為に長期間使用される屋外看板等には使用出来ない。
金色もブロンズ粉を使用した輝度の高い色は耐候性・耐薬品性が 弱い為、工業製品に金色の印刷をする場合にはアルミペースト+透明黄の調色で対応する。
この場合、ブロンズ粉と同等の輝度は得られない。
エポキシ樹脂ベースのインキは、強光沢の厚膜インキで接着性が非常に優れているが、屋外暴露により チョーキング現象を起こし光沢が低下する為、耐候性が要求される用途には使用されない。
高濃度白インキを屋外 で使用する印刷物に使用する際にも、チョーキング現象について考慮しなくてはならない。
このように耐性が必要な場合には、色の差、質感の差が出てしまうことを得意先に了解してもらうよう働きかけるべきである。
3.色差の意味するもの
色差Eのレベル分けとしては、一般に下表の様になっている。
色差(Ε) | 色差の程度 |
---|---|
〜0.8 | 目視判定の再現性から見て厳格な色差規格を設定できる限界 |
0.8〜1.6 | 隣接比較色差が感じられるレベル |
1.6〜3.2 | 離間比較では殆ど気づかない |
3.2〜6.5 | 印象レベルでは同じ色として扱える範囲 |
6.5〜13 | マンセル色票間の色差に相当 |
13〜 | 系統色で区別がつく程度の色の差 |
分光測色計を使用しても、目標の色に完全に一致させる事は非常に難しい。
つまり、許容範囲の設定が重要になってくる。
Εが1.2以上あればほぼ100%の人が差を感じるという説もあれば、一方同じΕが1.2以上でも約15%の人だけしか差を感じないという報告もある。
前に述べた個人差の問題である。
又人間の目は一般に、彩度の高い鮮やかな色(特にグリーン)についての判断が弱い。
彩度の高い鮮やかな色は、上表よりも大きな色差があって も目視では識別する事が難しい。
つまり分光測色計を使用して彩度の高い鮮やかな色について厳密な調色をしても、コストや時間の割には実用上はあまり意味がない事になる。
分光測色計の機械誤差、機種誤差も考えなければならない。
従って、色の許容差は、実用上の問題や測定機器の再現性等を十分に調査し、 合理的に決定する事が必要になってくる。
下表は、色の許容差を決定するときの目安である。
許容色差 | 程度 | 事例 |
---|---|---|
≦0.3 | 75%許容差(至難) | 測定機器の再現精度 |
≦0.6 | 50%許容差(厳密) | 実用的許容差の限度 |
≦1.2 | 5%許容差(実用) | 並置比較の実用許容差 |
≦2.5 | 印象レベル(実用) | 離間比較の実用許容差 |
≦5 | 容認(変退色評価) | 経時比較の実用許容差 |
≦10 | 色名レベル | 同一色名範囲 |
参考文献
- 印刷インキハンドブック 印刷インキ工業会(S53.6)
- スクリーン印刷インキの調色技術 東京都立工業技術センター(H4.10)
- その他